Saiba quais são os benefícios de uma manutenção planejada!
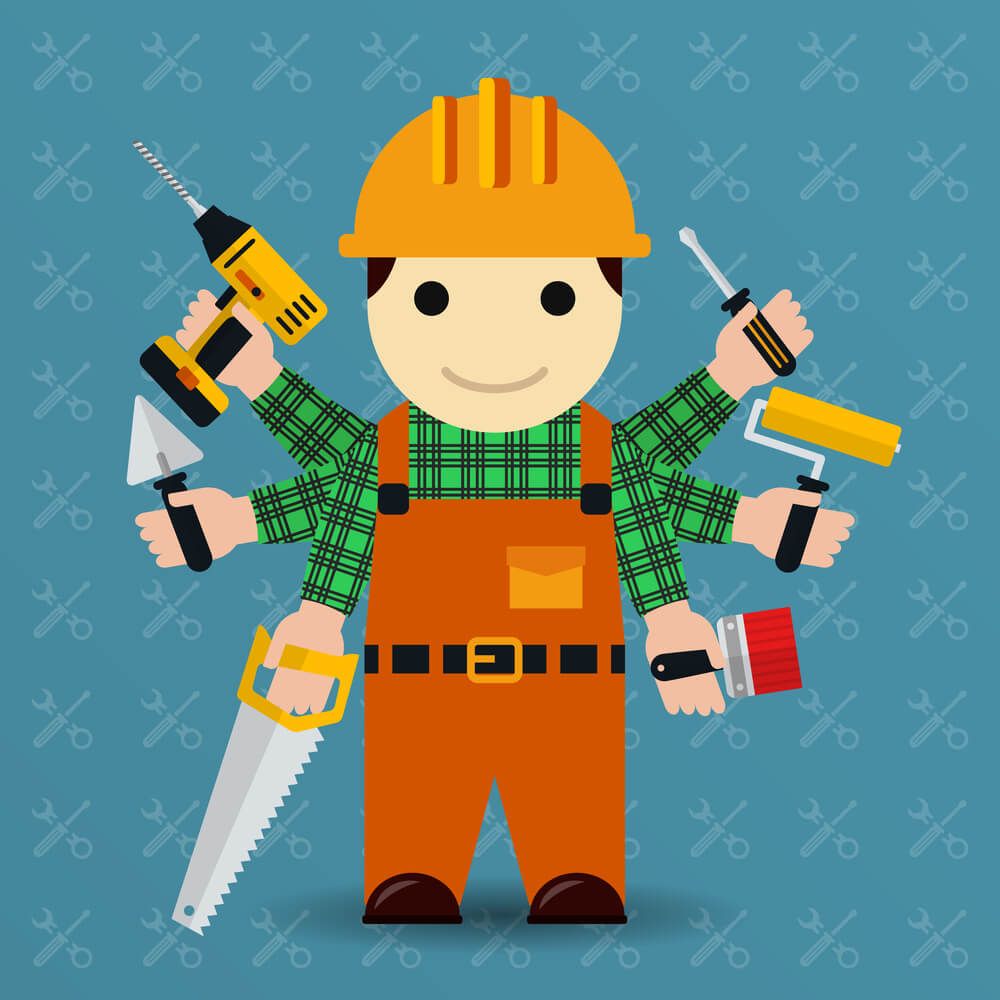
O termo manutenção tem a sua origem identificada nas palavras manter e conservar o estado de um objeto. Já no âmbito industrial moderno, a sua aplicação assume sentido mais amplo, como é o caso da manutenção planejada e de outras vertentes que atuam no processo produtivo.
Para compreender o seu real impacto, é preciso analisar as propriedades das máquinas e ferramentas. Afinal, todos os materiais envolvidos estão sujeitos ao desgaste e à deterioração no decorrer do tempo.
Quando isso acontece, o gestor tem duas opções: substituir a peça e arcar com os custos do investimento ou realizar a sua renovação por meio de reparos planejados.
Para saber como essa atividade funciona na prática, basta continuar lendo este artigo. Aproveite!
Quais são os principais tipos de manutenção?
A constante utilização das máquinas no processo produtivo leva ao seu desgaste, que pode causar defeitos nos itens fabricados. Para contornar esse cenário desfavorável, deve-se adotar a manutenção como uma estratégia para que as atividades permaneçam em constante melhoria.
Manutenção preventiva
Como o próprio nome sugere, o seu objetivo é evitar falhas e danos à produção que possam comprometer os resultados da área. Quando novos, os equipamentos são dimensionados de acordo com:
- a sua capacidade produtiva;
- o seu consumo de energia; e
- a sua estimativa de durabilidade.
Com essas informações em mãos, o gestor da área produtiva pode determinar qual é a frequência ideal para realizar a manutenção. Em geral, é instituído um check-list com todos os itens a serem verificados e os respectivos intervalos de tempo.
Além da mensuração por tempo, é possível programar as revisões de acordo com o número de horas que o equipamento permanece em utilização. Essa programação pode considerar dados históricos sobre o funcionamento de cada ativo para reduzir a probabilidade de falhas.
Como resultado, a incidência de gastos excessivos devido à paralisação da produção é minimizada, e o controle contínuo aumenta a eficiência.
Manutenção produtiva total
Esse é um conceito muito importante na indústria, em especial para aquelas que adotam a produção enxuta. O termo tem origem na expressão em inglês Total Productive Maintenance (TPM), cujos princípios são:
- a melhoria das pessoas;
- a melhoria dos equipamentos;
- a qualidade total.
Essa técnica tem caráter corretivo e preventivo, pois busca aumentar a eficiência da linha de produção como um todo, além de garantir a conservação de todos os materiais envolvidos.
Como resultado, pode-se observar a redução nas perdas, a diminuição do número de paradas e a queda dos custos operacionais. A sua execução é extremamente abrangente porque inclui todas as áreas e colaboradores para o alcance de um objetivo comum.
Manutenção não planejada
Esse tipo de atividade é realizado quando já foi constatada a queda no desempenho dos recursos ou houve interrupção da produção por causa de um defeito que se manifestou subitamente. O seu propósito é corrigir a falha o mais rápido possível para evitar consequências mais graves.
Um dos principais desafios dessa modalidade é que não há tempo para o planejamento da realização dos reparos. Com isso, os componentes necessários podem não estar disponíveis de imediato, o que resulta em atrasos. Além disso, a aquisição de peças para substituição é emergencial, o que pode acarretar em preços elevados.
Manutenção planejada
O seu significado pode ser interpretado como a realização de verificações de todos os elementos vinculados à produção. Além disso, é essencial garantir a qualidade dos produtos por meio da prevenção de prováveis falhas ou quebras dos elementos das máquinas.
Nesse caso, o objetivo pode ser descrito como a conservação de equipamentos, peças e máquinas em condições de pleno funcionamento para garantir a produtividade.
A etapa de planejamento fica por conta da programação da parada da produção, da aquisição dos materiais necessários e da disponibilização de profissionais para conduzir essa tarefa.
Isso quer dizer que a decisão de executar uma manutenção de natureza planejada envolve diversas áreas que devem coordenar os seus esforços para que os resultados sejam positivos.
Como efeito, os recursos produtivos operam com maior eficiência por mais tempo.
Quais são as vantagens da manutenção planejada?
Um dos principais benefícios é a viabilização da redução de custos com a realização de reparos emergenciais e a interrupção da operação por causa de falhas. Devido ao seu significativo impacto sobre a qualidade das mercadorias, é recomendado que a área produtiva dedique tempo e recursos para garantir o perfeito funcionamento do maquinário e das ferramentas.
Calor, excesso de peso e produtos químicos são responsáveis por desgastar máquinas e equipamentos, comprometendo, assim, a sua utilização. A manutenção planejada constitui uma solução viável para ampliar a vida útil do aparato produtivo.
Independentemente do porte da sua empresa, é visível como esse tipo de manutenção ajuda a assegurar a qualidade dos produtos e, consequentemente, o fluxo de entrada de receitas de vendas.
Essa é uma estratégia que demonstra obter diversos resultados favoráveis. Entre os quais, pode-se citar:
- evita a perda financeira;
- diminui a insatisfação dos clientes;
- previne atrasos nas entregas; e
- evita produtos com defeito de fabricação.
Qual é a importância da gestão da manutenção?
Com a crescente busca da qualidade dos produtos e a competição no mercado, é preciso desenvolver formas de tornar o processo produtivo cada vez mais eficiente. Muitas empresas deixam de lado a atividade de manutenção e aumentam os riscos de problemas com a sua operação.
Para prevenir essa situação, é necessário estabelecer planos para que o rendimento das máquinas não seja penalizado ou interrompido devido à falta de inspeções e reparos periódicos.
Por esse motivo, é fundamental implementar a gestão da manutenção, para que seja possível:
- organizar as informações disponíveis;
- arquivar a documentação técnica pertinente;
- garantir a adequação do espaço físico da fábrica;
- recrutar profissionais dedicados a essa atividade;
- manter registros atualizados do processo de manutenção;
- desenvolver ferramentas personalizadas em caso de necessidade.
Para aumentar a durabilidade dos recursos de produção, é preciso adotar projetos de gestão fabril para garantir que a produtividade e a lucratividade sejam mantidas em constante crescimento. A manutenção planejada é uma das soluções para obter um controle rigoroso do desgaste do maquinário e prevenir falhas.
Você quer ter acesso a mais conteúdos como este? Então, siga-nos nas redes sociais: Facebook, LinkedIn, Twitter e YouTube.