Veja o que é e quais os benefícios do fluxo contínuo
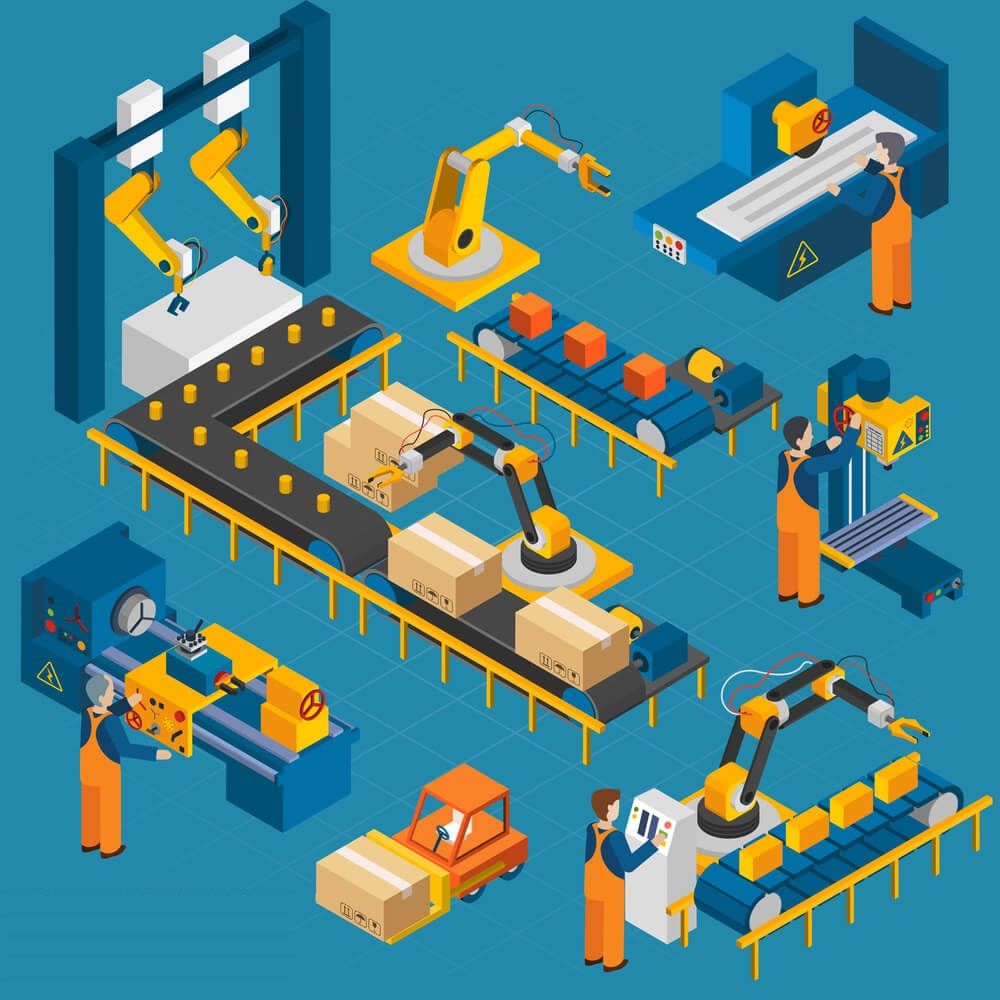
A indústria manufatureira deve estar sempre em busca de melhoria em seus processos. Nesse sentido, um modelo bastante eficaz é o fluxo contínuo de produção. Além de diminuir o tempo gasto para produzir cada item, ele ainda pode reduzir os custos e otimizar a utilização de matéria-prima.
Neste artigo, vamos falar sobre como surgiu esse modelo e como ele é utilizado na indústria. Além disso, vamos mostrar as principais vantagens de quem opta por esse caminho. Então, fique atento e boa leitura!
O que é e como surgiu o fluxo contínuo?
Para entender melhor o conceito, vamos conhecer a história por trás dele. Confira, a seguir, como ele surgiu.
Ford
Na década de 1910, Henry Ford revolucionou a indústria manufatureira ao criar um sistema de produção inovador. Na época, ele precisava reduzir o tempo de produção de seus veículos para aumentar a capacidade de produção.
Para tanto, ele criou uma linha de montagem, na qual cada veículo era montado do início ao fim por meio de uma sequência de etapas. Então, as peças eram acrescentadas ao carro à medida em que ele percorria a esteira rolante.
Por meio dessas medidas, Ford conseguiu reduzir o tempo de montagem de cada unidade de 12 horas para apenas 90 minutos. Ademais, houve uma redução de 50% nos custos da produção.
Toyota
Anos mais tarde, já na década de 1950, a Toyota implementou um novo padrão de produção. O modelo fordista funcionava apenas para produção em massa e precisava de um grande volume de estoque.
Para conseguir produzir em menores quantidades, ela desenvolveu um processo onde cada unidade é produzida do início ao fim de forma contínua. Isso significa que os produtos acabados são fabricados apenas sob demanda (Just In Time).
Além disso, a qualidade é verificada a cada etapa, o que evita desperdícios e refações. Com isso, há uma redução do tempo total de produção, bem como dos custos.
Conceito atual
O conceito de fluxo contínuo reflete a teoria toyotista. As unidades são fabricadas individualmente por meio de um processo ininterrupto. Para isso, é utilizada a ideia de Just In Time. Ou seja, a necessidade de estocagem de matéria-prima é eliminada.
Como ele é implementado na indústria?
Na prática, o fluxo contínuo requer uma série de alterações com relação ao modelo tradicional de produção.
O primeiro ponto importante é que os processos precisam ser totalmente estáveis. Outro quesito que requer atenção é que não se deve produzir em lote. A ideia é otimizar o processo por meio da produção individual.
As únicas exceções são as etapas em que é necessário realizar uma mudança significativa no maquinário entre uma peça e outra.
Com relação às etapas de implementação do modelo, temos:
- definição das famílias de produtos;
- alinhamento das famílias na sequência de produção;
- observação e verificação da qualidade em cada etapa.
É importante lembrar que qualquer discrepância percebida deve ser corrigida antes de dar prosseguimento ao processo. É isso que garante a máxima eficiência do modelo.
A adequação do layout do maquinário e da qualificação da equipe também é fundamental para o sucesso do fluxo contínuo. Cada funcionário deve ser capaz de operar diversas máquinas, e estas devem estar dispostas em ordem, de acordo com o fluxo do processo.
Quais os benefícios desse modelo de produção?
O uso do fluxo contínuo no processo de produção pode proporcionar diversas vantagens à indústria. Vamos destacar as 3 principais delas. Confira!
Redução de tempo de produção
A fabricação individualizada dos produtos reduz o tempo gasto desde a produção até a entrega ao cliente.
Suponha que você seja dono de uma fábrica de bancos para carros e que estas sejam as etapas da produção:
- montagem da estrutura;
- corte das espumas;
- corte dos tecidos;
- costura e acabamento.
No modelo tradicional, os insumos são produzidos em lotes. Digamos que sua fábrica produz em lotes de 50 unidades. Nesse caso, as demandas menores que 50 bancos gerarão um estoque de matéria-prima.
No fluxo contínuo, apenas o que foi demandado é produzido. Sendo assim, se forem encomendados 10 bancos, serão fabricados 10 insumos. Ou seja, sem a utilização de tempo sobressalente.
Redução de custos
Os custos de produção no fluxo contínuo são otimizados de forma que é gasto apenas o necessário para cada demanda. Dessa forma, o controle sobre os insumos é maior. Além disso, as aferições de qualidade mais rigorosas ajudam a evitar desperdícios.
Voltando o exemplo anterior, no modelo antigo, só após a produção final de todos os bancos é que se teria a certeza de que tudo saiu conforme o planejado. Desse jeito, o retrabalho para realizar correções seria muito maior, e, consequentemente, os custos e os riscos de perdas também.
Já no fluxo contínuo, os problemas são identificados a cada etapa. Assim, a correção é mais fácil e rápida. Isso evita o desperdício de materiais e ajuda na recuperação de defeitos.
Otimização do processo para produtos diversificados
Dependendo da situação, um dos grandes pontos positivos da produção em lotes pode ser, também, um dificultador. Para projetos fechados ou produtos sem variações, o modelo tradicional é válido. Caso contrário, a entrega em maior escala é mais vantajosa no fluxo contínuo.
Se, no caso dos bancos, por exemplo, os modelos de carros mudam a cada ano, a demanda tende a diminuir. Com isso, os estoques de insumos podem acabar se tornando obsoletos com o passar do tempo.
Por outro lado, no fluxo contínuo, a produção é focada na demanda. Tem demanda, tem produção. Não tem demanda, não tem produção. Assim, quando um produto é modificado, a capacidade de adaptação é muito maior e os riscos de prejuízo, bem menores.
Enfim, adotar o modelo de fluxo contínuo da produção manufatureira pode ser desafiador, mas proporciona benefícios significativos. Antes de tomar uma decisão assim, é preciso conhecer bem os processos e fazer um bom planejamento.
E por falar nisso, que tal saber tudo sobre o assunto? Confira o que é o planejamento de produção industrial e qual a sua importância. Nunca deixe de buscar saber sempre mais sobre tudo o que envolve produtividade!